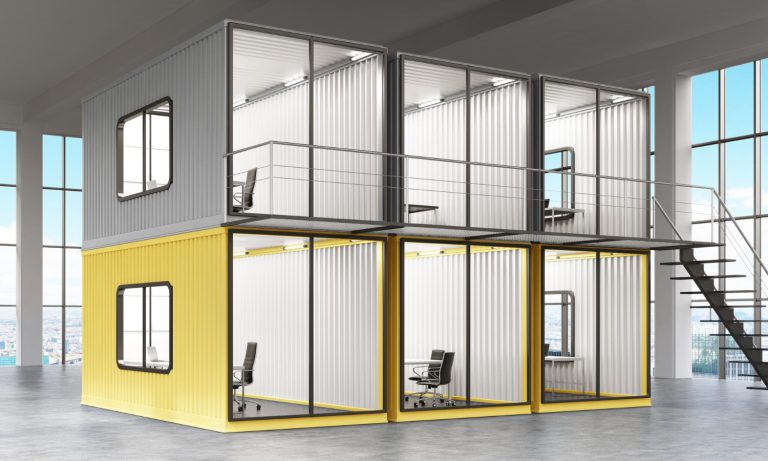
As Malaysia’s construction industry evolves, modular construction emerges as a transformative force, redefining efficiency, sustainability, and project timelines. This method, which involves prefabricating building components off-site before assembly, is gaining traction due to its ability to address labour shortages, reduce waste, and accelerate project completion.
The Malaysian government has actively encouraged the adoption of Industrialised Building Systems (IBS), a category that includes modular construction, through policies such as the Construction 4.0 Strategic Plan and the IBS Roadmap 2021-2025, aiming aim to modernise the sector by integrating automation, robotics, and digitalisation into construction workflows.
Several major players, including Gamuda, Sunway Construction, and MGB Berhad, have embraced modular techniques. For instance, Gamuda’s Digital IBS facility produces exact modular components, reducing reliance on manual labour and enhancing quality control. Meanwhile, MGB’s IBS precast plant has delivered modular high-rise projects, significantly reducing construction time.
Additionally, the Malaysian government intends to implement innovative construction technologies under the 12MP to achieve its sustainability goals, such as:
- Industrialised Building Systems (IBS): Manufacturing building components in a controlled environment minimises waste and increases energy efficiency, resulting in lower embodied carbon output during construction operations.
- Prefabricated Prefinished Volumetric Construction (PPVC): Building modules are constructed off-site and transported for assembly, cutting construction time and disruptions and ensuring precision and quality control. This translates into energy savings and lower emissions.
- BIM (Building Information Modelling): A digital representation of a facility’s physical and functional properties. BIM enables improved planning, design, and management. This strategy uses resources and energy more efficiently, identifies potential challenges early in the design process, and avoids errors and rework, contributing to lower carbon emissions.
- Modular Construction: Building pieces are assembled at a factory before being transported for installation. This increases efficiency and sustainability by shortening building time, decreasing material waste, and lowering on-site energy use. Modular approaches facilitate the application of energy-efficient technologies and designs.
Malaysia’s strategy is also aided by incentives to promote the application of technologies such as IBS, BIM, and modular building. These incentives are intended to encourage mechanisation and automation in the construction industry, accelerate project completion, assure resource and cost-effectiveness, and reduce reliance on low-skilled workers.
Globally, modular construction is expected to grow at a CAGR of 6.9% from 2021 to 2028, and Malaysia is poised to be a regional leader in this shift. However, challenges remain, including high initial investment costs and industry-wide resistance to change. Overcoming these barriers will require stronger collaboration between developers, policymakers, and technology providers.
With continued innovation and policy support, modular construction is set to play a key role in Malaysia’s infrastructure development, delivering high-quality, sustainable buildings faster than traditional methods.