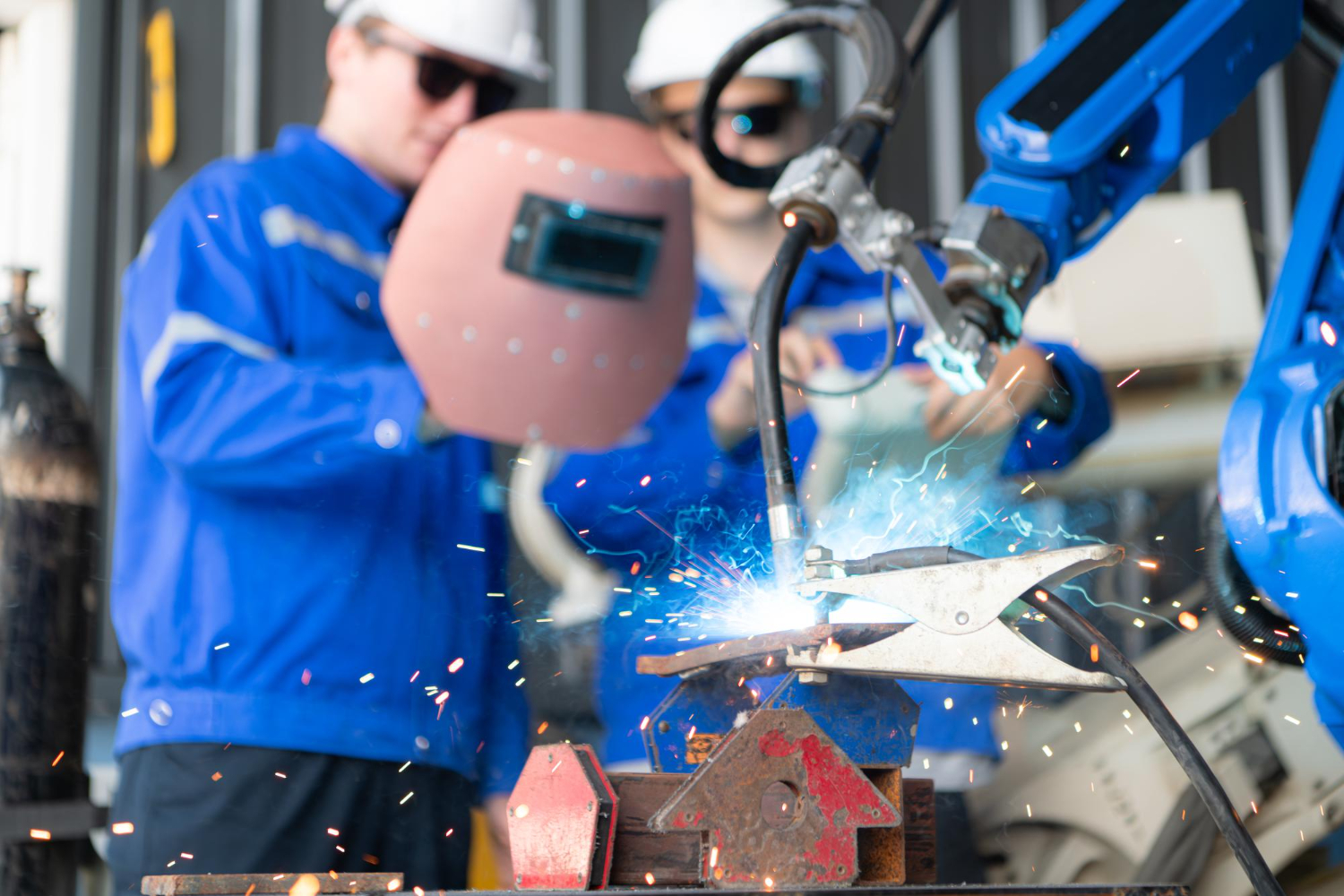
The integration of robotic welding in construction is transforming the industry, bringing unprecedented levels of efficiency, precision, and safety. Unlike humans, robotic welding arms can work continuously without breaks, holding torches and performing welds quickly and accurately. This ability is beneficial for repetitive tasks and in various challenging environments.
One significant advancement in robotic welding is the use of automated systems that are programmable and adaptable to different materials and tools. For instance, systems like Yaskawa’s robust rotary torch combined with their Universal Weldcom Interface (UWI) facilitate high-production cladding with minimal programming requirements, enhancing production efficiency.
Robotic welding systems are also being designed to assist human welders. Collaborative robots, or cobots, can handle dangerous tasks such as holding materials in place, allowing human workers to focus on more intricate welding tasks. This collaboration improves safety and boosts overall productivity on construction sites.
Mobile robotic welding systems, such as those showcased by Productive Robotics, can be deployed to different locations for on-site fabrication. These systems, like the Blaze robotic laser welder, are significantly faster than traditional TIG welding, providing high-strength joints with minimal wire consumption. Such innovations ensure that construction projects are completed more quickly without sacrificing quality.
Additionally, integrating the Internet of Things (IoT) and data analytics in welding processes is becoming more prevalent. These technologies enable enhanced monitoring and quality control, providing real-time data for welders to adjust techniques and settings. Predictive maintenance, powered by data analytics, reduces downtime and increases the lifespan of welding equipment.
Safety innovations are also at the forefront of robotic welding advancements. Enhanced personal protective equipment (PPE), including helmets with augmented reality (AR) capabilities and sophisticated ventilation systems, ensure a safer working environment for welders. The synergy between 3D printing and welding creates new opportunities in custom fabrication, particularly in sectors like automotive and aerospace, where intricate designs and rapid prototyping are essential.